|
Электронная версия
научно-популярного журнала "Архитектура и
строительство Москвы".
Выходит 6 раз в год.
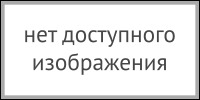
Содержание
номера:
А. П. Кудрявцев
Проект и реализация
- гаранты безопасности среды жизнедеятельности
В.И. Ресин
Обеспечение
безопасности - первостепенная задача
градостроительного комплекса столицы
В. М. Бондаренко
К вопросу о
конструктивной безопасности и живучести
строительного основного фонда России
Ю. А. Сдобнов
Город как система
рисков
Ю. П. Панибратов
Проектирование и
строительство в условиях Санкт-Петербурга
А В. Анисимов
Архитектура как
форма гарантии интеллектуальной безопасности
Л. В. Хихлуха
Жилищное
строительство: уроки прошлого и задачи
настоящего
С. М. Лыжин
Возрастная
структура населения в домах массового жилищного
строительства
Н. И. Карпенко, В. Н.
Ярмаковский
О ресурсном
обеспечении национального проекта "Доступное
и комфортное жилье - гражданам России"
С. Г. Головнев
Обеспечение
качества и безопасности возводимых зданий
средствами строительных технологий
Ю. А. Табунщиков
Строительные
концепции зданий XXI века в области
теплоснабжения и климатизации
Медали и дипломы РААСН
Ю.С. Янковская
К истории
несостоявшейся школы
В. А. Соловьев
Красные ворота
Я. Ш. Каждан
Вадим Григорьевич
Макаревич |
Для успешной реализации данного проекта
необходимо организовать дополнительно
производство и использование не менее 60 млн. м3
бетона и железобетона в год. При этом
технико-экономические показатели бетона и
конструкций из него должны быть значительно
выше, чем в настоящее время, чтобы снизить
стоимость строительства минимум на 20% и
одновременно обеспечить должную комфортность
возводимого жилья.
Одним из наиболее рациональных и эффективных
путей решения названной задачи способно стать
комплексное применение в конструктивных
системах жилых зданий модифицированных легких
бетонов различных видов и назначения, получаемых
преимущественно на базе продуктов переработки
крупнотоннажных техногенных отходов и местных
природных материалов. Здесь возможно достигнуть
значительной экономии энергоресурсов за счет
объемов работ в карьерах для добычи природных
заполнителей, глин, известняка.
Приготовление бетона в указанных масштабах
потребует дополнительно около 25 млн. тонн
цемента и более 50 млн. м3 крупного заполнителя,
энергоемкость и стоимость которых должны быть
существенно ниже, чем у применяемых в настоящее
время, а требуемые показатели качества - по
меньшей мере не ниже.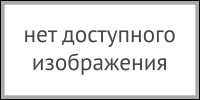
Как показывают расчеты (в статье мы вынуждены их
опустить), все это вполне осуществимо минимум для
2/3 регионов России, если рационально
использовать сырьевую базу крупнотоннажных
техногенных отходов (прежде всего черной и
цветной металлургии, тепловой энергетики) и базу
местных природных материалов (в частности,
пористых горных пород вулканического и
осадочного происхождения). Необходимым условием
является наличие или ввод в действие
соответствующих производственных мощностей по
переработке данных материалов в эффективные
компоненты бетона (вяжущие и заполнители).
Вышеупомянутое снижение энергоемкости и
стоимости возведения жилых зданий не менее чем
на 20% может быть реально достигнуто к 2010 году при
условии реорганизации технологической
структуры строительной индустрии в следующих
основных направлениях:
- замена в бетоне заполнителей соответственно из
плотных горных пород или высокоэнергоемкого
керамзита на преимущественно безобжиговые или
существенно менее энергоемкие пористые,
получаемые путем переработки техногенных
отходов, или на модифицированный
низкоэнергоемкий керамзит, или на местные
заполнители из пористых горных пород:
энергоемкость производства таких заполнителей
меньше в 2-10 раз, а себестоимость ниже в 1,5-5 раз;
- увеличение доли шлакопортландцемента в общем
объеме производства цементных вяжущих с
сегодняшних 6% до минимум 25%, а доли
портландцемента с активными минеральными
добавками (АМД) на основе продуктов переработки
техногенных отходов или вулканических пород - с
44,5% до 60-70%; при этом содержание АМД в цементах
следует повысить с 20% (по отечественным нормам) до
35% (в соответствии с европейскими нормами EN - 1,2:
2000);
- предельно возможная рациональная замена
цементных вяжущих в теплоизоляционных и
конструкционно-теплоизоляционных бетонах на
малоклинкерные композиционные или смешанные
вяжущие (КВ), изготовляемые на базе химически
взаимосочетаемых техногенных отходов или
гидравлически активных вулканических пород;
энергоемкость этих вяжущих типа так называемых
"тонкомолотых многокомпонентных цементов"
(ТМЦ) или вяжущих низкой водопотребности (ВНВ)
ниже на 15-55%, стоимость меньше на 14,5-24%, а
показатели теплотехнического качества
существенно выше.
За последние 20 лет разработаны и успешно
эксплуатируются ряд отечественных технологий по
переработке техногенных отходов текущего выхода
в эффективные пористые заполнители различных
классов для теплоизоляционных,
конструкционно-теплоизоляционных и
конструкционных легких бетонов. Отметим только
наиболее востребованные, отличающиеся
экологической чистотой, низкой энергоемкостью,
высоким качеством продукции и соответствующие
(или даже превосходящие) уровню мировых аналогов:
- технология производства пористого гравия со
стекловидной оболочкой (шлакостеклогранулят -
ШСГ) из доменных и ферросплавных шлаков текущего
выхода, внедренная на Новолипецком
металлургическом комбинате в 1999 году;
шлакостеклогранулят в регионе изготовления
близлежащих областях в 2-3 раза дешевле
гранитного щебня и в 3-5 раз - керамзитового гравия
при высоких показателях качества;
- технология производства пористого гравия на
основе шлакозольных отходов ТЭС текущего выхода
- шлакозита; технология внедрена в 1990 году на
Тольяттинской ТЭС; энергозатраты в 2 раза, а
себестоимость - в 1,5 раза ниже, чем при
изготовлении керамзита, теплотехнические же
показатели значительно выше;
- технология производства пористого гравия типа
керамзита на основе отходов углеобогащения;
благодаря использованию несгоревшей части
топлива (до 15%), энергозатраты на изготовление
такого заполнителя и его себестоимость меньше в
1,5 раза, чем для традиционного керамзита;
технология внедрена в 1989 году на Интинской
углеобогатительной фабрике.
Следует отметить, что в последние 20 лет за
рубежом прослеживается явная тенденция к
наращиванию производства пористых заполнителей
как в целом, так и особенно на базе использования
крупнотоннажных техногенных отходов. По данным
Task Group TG 8.1 fib-2004 (Lightweight Aggregate Concrete), SINTEF (Norway), CANMET
(Canada), доля этих материалов в общем объеме
производимых заполнителей для легких бетонов
составляет в среднем 25,5%; планируется за
ближайшие 10 лет повысить ее в 1,5-2 раза. В
отдельных странах Западной Европы она уже сейчас
достигает 50%. В России соответствующий
показатель - менее 5%. В то же время имеются все
предпосылки для освоения рассматриваемых
технологий во многих регионах страны (при
должном научном и проектном сопровождении их
реализации). Так, изготовление
шлакостеклогранулята реально освоить на
одиннадцати крупных металлургических
предприятиях в объеме свыше 14 млн. м3 в год,
шлакозита - на семнадцати ТЭС в объеме свыше 18
млн. м3 в год, керамзита на основе углеотходов - на
двадцати двух углеобогатительных фабриках в
объеме свыше 15 млн. м3 в год. Срок окупаемости
работ по внедрению технологических линий
производительностью от 100 до 300 тыс. м3
заполнителя в год при общей стоимости 0,75 - 1,5 млн.
долларов - не более двух лет.
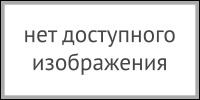
Согласно данным Всероссийского геологического
фонда, разведанные запасы горных пород
вулканического и осадочного происхождения по
Дальневосточному, Восточно-Сибирскому округам
(вулканические шлаки, пемзы, пористые базальты,
туфы) и по Северо-Кавказскому округу
(вулканические шлаки, туфы, пористые карбонатные
породы) составляют около 1,5 млрд. м3. Имеющийся
опыт показывает, что на их базе возможно
производить низкоэнергоемкие,
высококачественные и экономически чистые
пористые заполнители для легких бетонов в
количестве 30 млн. м3 в год, обеспечив ими
строительство жилья в этих округах примерно на 50
лет.
Суммируя вышесказанное, мы вправе
констатировать: задача получения дополнительных
50 (и более) млн. м3 пористых заполнителей реально
выполнима, причем обеспечены ими могут быть
строительные комплексы подавляющего
большинства регионов страны.
Следует также иметь в виду довольно значительный
и в то же время крайне мало востребованный
резерв: отходы цветной металлургии. Речь идет о
шлаках медно-никелевого производства.
Гранулированные шлаки можно использовать для
изготовления мелкого заполнителя, литые
охлажденные - для плотного щебня. Имеется
необходимая технология, успешно прошедшая
апробацию на ряде предприятий Уральского округа.
Потенциальный выход продукции - заполнителей,
превосходящих по своим качествам природные, -
свыше 13 млн. м3 в год.
Основными и наиболее реальными путями
реализации задачи наращивания годового объема
производства цемента в ближайшие 3 года не менее
чем на 25 млн. т в год представляются повышение
доли выпуска шлакопортландцемента (ЩПЦ) минимум
в 4 раза и портландцемента с активными
минеральными добавками (или многокомпонентных
цементов) - минимум в 1,5 раза. Достигнув этого
(необходимые сырьевые ресурсы у нас имеются),
отечественная промышленность по структуре
производства цементных вяжущих вплотную
приблизилась бы к наиболее "продвинутым" в
указанном отношении странам. Так, по данным PCA, в
Южной Корее из 53 млн. т получаемых в год цементных
вяжущих шлакопортландцемент составляет 10 млн. т
(18,8%), в Индии соответственно из 100 млн. т - 35 млн. т
(35%), в Японии из 76 млн. т - 17 млн. т (22,4%). Europeans Slag и
CEMBUREAU-2005 называют такую цифру: доля производства
ШПЦ в государствах Европы с развитым доменным
производством (Германия, Франция, Испания,
Австрия, Швеция) - 37% (в Нидерландах - более 50%) и
прослеживается явная тенденция к ее росту.
Говоря о перспективах увеличения доли
производства многокомпонентных цементов,
следует заметить, что выпускается их (с
содержанием активных минеральных добавок до 35%) в
ряде развитых стран более 70% от общего количества
цементных вяжущих. Есть сырьевые ресурсы для
достижения такой отметки и в России. Практически
уже начат переход к европейским стандартам (и
качественным, и структурным) изготовления
цемента на заводах ОАО "Альфацемент". Они
производят сегодня цемент с добавкой 29,5% шлака
СЕМ 11/В-Ш32,5 (ШПЦ), отвечающий высоким требованиям
европейских норм на цементы EN 197-1,2: 2000; его доля в
общем объеме выпуска вяжущих составляет свыше 20%,
причем планируется дальнейшее наращивание этого
показателя.
Еще в 1980-х годах в СССР были разработаны
принципиально новые многокомпонентные цементы,
производство которых позволяло экономить от 50 до
70% клинкера практически без ухудшения основных
строительно-технических свойств относительно
бездобавочного портландцемента. Имеются в виду
такие композиционные малоклинкерные вяжущие,
как тонкомолотые многокомпонентные цементы ТМЦ40
и ТМЦ50, получаемые при совместном помоле
портландцемента с золой уноса, вулканическим
шлаком, перлитом, доменным граншлаком и тому
подобными, а также вяжущие низкой
водопотребности ВНВ-30 и ВНВ-50 - те же компоненты
плюс порошкообразный суперпластификатор С-3.
Однако заводы отказались от освоения их
массового выпуска в связи с недостаточной
востребованностью тогда строительным
комплексом. В настоящее время нужда в
композиционных малоклинкерных вяжущих (КВ) в
связи с повышением требований к теплозащитным
свойствам ограждающих конструкций вполне
достаточна. Тем не менее, сегодня наиболее
целесообразно - технически и экономически -
производить их не на цементных заводах (которые у
нас, кстати, находятся отнюдь не в блестящем
состоянии, о чем надо говорить отдельно), а на
специальных технологических линиях крупных
предприятий стройиндустрии (КПД, ДСК),
изготавливающих на основе этих вяжущих легкие
бетоны для стеновых изделий. Там же можно
производить КВ как непосредственно для своих
нужд, так и для снабжения других предприятий
стройиндустрии региона или возводимых объектов.
Приведенные рекомендации тем более
целесообразны, что, по данным Общественного
Совета по жилищной политике при
Минрегионразвития РФ (декабрь 2005) из 400-500
имевшихся в 1990 году ДСК сейчас в стране
функционирует лишь 100-120, а в полную силу работают
лишь 20-30.
На текущий момент в РФ доля производства КВ или
смешанных вяжущих с содержанием клинкера менее
50% составляет максимум 2% от общего объема
производства цементных вяжущих, тогда как за
рубежом она доходит до 25% в Европе и до 35% в США и
Канаде. Особенно эффективна для
теплоизоляционных и
конструкционно-теплоизоляционных легких
бетонов такая разновидность КВ, как вяжущие
низкой водопотребности (ВНВ), изготовляемые на
основе доменного граншлака: при содержании
клинкера 25-30% цементный камень ВНВ имеет
коэффициент теплопроводности на 30-35%,
сорбционную влажность - на 40-45%, а усадку - на 20-30%
меньше, чем портландцементный камень.
Использование этого вида вяжущего позволило
создать уникальный вид теплоизоляционного
бетона - модифицированный полистиролбетон,
который по комплексу технико-экономических и
теплотехнических показателей превосходит
традиционные плитные утеплители.
Важно отметить, что утилизация техногенных
отходов при производстве бетона и железобетона
будет способствовать решению актуальных
экологических проблем в индустриально развитых
регионах России (переработка самих отходов,
сокращение объема отвалов, высвобождение
дополнительных площадей для
сельскохозяйственных угодий и другие
благоприятные факторы). Значительного эффекта
следует ожидать от комплексного использования в
массовом строительстве жилья легких бетонов
нового поколения на рассмотренных выше вяжущих и
заполнителях, изготавливаемых на основе
продуктов переработки техногенных отходов и
местных природных материалов (в частности,
пористых горных пород). Этот эффект выражается в
основном в следующем:
- снижение массы здания до 30% и соответствующее
уменьшение расходов на устройство фундаментов;
- повышение уровня тепловой защиты (до 20%) за счет
увеличения теплотехнической однородности
"оболочечной" системы зданий (или системы
ограждающих конструкций), когда на "теплые
стены" из особо легких теплоизоляционных
бетонов выходят элементы из конструкционных
легких бетонов с меньшей в 2-3 раза по сравнению с
тяжелым бетоном теплопроводностью;
- повышение тепловой устойчивости ограждающих
конструкций за счет замены традиционных плитных
утеплителей на теплоизоляционные легкие бетоны
с существенно (до трех раз) большим коэффициентом
теплоусвоения; отсюда - обеспечение стабильности
микроклимата в жилых помещениях даже при
возможных аварийных ситуациях;
- повышение надежности тепловой защиты зданий за
счет существенно большей долговечности и
обеспеченности во времени эксплуатации
теплофизических характеристик
теплоизоляционных бетонов в сравнении с
плитными утеплителями;
- повышение надежности и эксплуатационной
безопасности (прежде всего, пожаростойкости) за
счет более высокой огнестойкости несущих
легкобетонных конструкций в сравнении с
аналогичными конструкциями из тяжелых бетонов.
Кратко повторим и подытожим сказанное. Итак, в
нашей стране имеется обширная сырьевая база
многотоннажных техногенных отходов и местных
природных материалов, вполне достаточная для
производства заполнителей и вяжущих в требуемом
для реализации национального проекта
"Доступное и комфортное жилье - гражданам
России" объеме; разработаны и успешно
апробированы технологии их изготовления,
приобретен опыт применения в жилищном
строительстве бетонов на их основе с высокими
показателями качества. Особенно эффективны
здесь легкие бетоны нового поколения (от
сверхлегких теплоизоляционных до
конструкционных высокопрочных). Стоимость
строительства при комплексном их использовании
может быть снижена минимум на 30% (одновременно
обеспечивается комфортность возводимого жилища
и решение ряда актуальных экологических проблем,
энергоемкость - минимум на 20%, а
энергопотребление зданий - минимум на 15%.
Для широкого распространения по регионам России
вышеназванных технологий целесообразно
создание Федеральной целевой программы (как
подпрограммы национального проекта), в рамках
которой следует предусмотреть научное и
проектное сопровождение процесса
порегионального внедрения с учетом специфики
ресурсных и климатических условий на местах. В то
же время необходимо отметить прогрессирующую
неадекватность состояния развития строительной
индустрии и строительной науки. Если первая
развивается стремительно, бурно, то вторая
влачит жалкое существование. Государство
отказывается от поддержки
научно-исследовательских организаций, а
стройбизнес не проявляет должной
заинтересованности в их деятельности,
довольствуясь давнишними, порой и вовсе
устаревшими технологиями. В результате
строительство зданий и сооружений зачастую
начинается без соответствующих
исследовательских и проектных проработок, что
приводит к многочисленным аварийным ситуациям.
Без коренного изменения ситуации реализовать
национальный проект "Доступное и комфортное
жилье" будет затруднительно, в том числе в
плане ресурсного его обеспечения.
|